FLUTE MANUFACTURING
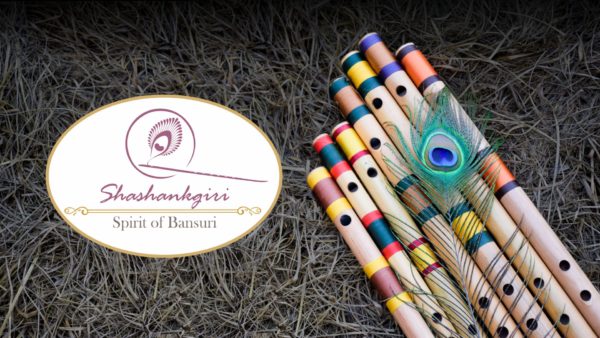
Bamboo flute manufacturing involves the process of creating flutes from bamboo, a natural material known for its resonance and suitability for crafting musical instruments. Bamboo flutes have a unique and soothing sound and are popular in various musical traditions around the world. The manufacturing process for bamboo flutes is often simpler than metal flutes, but it still requires skill and attention to detail to produce high-quality instruments.
There are majorly two types of flutes used in presenting Indian classical music.
1. Bansuri: The Bansuri is one of the most widely recognized flutes in India. It is a side-blown bamboo flute with six or seven finger holes. Bansuri is commonly associated with North Indian classical music and is used in various other genres as well.
2. Venu: Venu is a South Indian bamboo flute used in Carnatic music. It is shorter than the Bansuri and has eight finger holes, allowing for a wide range of pitches and intricate ornamentation.
Here are some general steps involved in bamboo flute manufacturing –
Bamboo selection: High-quality bamboo is essential for creating good-sounding flutes. At Shashank Giri Flutes, Best bamboos are sourced from the hilly regions of Assam by highly trained and skilled bamboo dealers. these bamboo dealers are given specific instructions to fetch a particular breed of finest quality of very long lasting bamboos. Bamboos with round or slightly oval shape is highly preferred to manufacture hing quality flutes. Mature and seasoned ( at least 3 years old) bamboo stalks with the appropriate diameter and thickness. Every pitch demands it own unique diameter. The whole process of making the flute is dependent on – accurately choosing the required diameter of bamboo for making the flute of desired pitch. The selected bamboo stalk is cut to the desired length depending on the pitch of flute being made.
Crafting finger holes: finger holes are drilled or burned into the bamboo. The placement and size of these holes determine the flute’s pitch and scale. the placement of the holes are on very high accuracy, as much as even a millimetre of miss calculation will cause the flute to go waste. The exterior of the bamboo flute is shaped and sanded for comfort and aesthetics. Tuning may involve adjusting the size and position of finger holes to achieve the desired pitch and tuning. All the notes are tuned keeping “A” 440Hz as a standard reference.
Threading of bamboo: The threading process involves wrapping fine silk or nylon threads around the flute. Bamboo is a natural material that can be susceptible to cracks or splitting, especially at the ends. Threading helps reinforce the nodes, adding strength and stability to the flute. It prevents the bamboo from expanding or contracting too much with changes in humidity, reducing the risk of cracks and maintaining the overall structural integrity of the instrument. Threading adds a decorative element to the bamboo flute. We use threads of various colours and materials, enhancing the visual appeal of the Bansuri and making it stand out as a unique and artistic instrument. In some cases, threading can help prevent or minimise cracks that may develop in the bamboo due to the stresses placed on it during playing or changes in environmental conditions. Threading, when done properly, can enhance the performance and lifespan of the bamboo flute, making it a valued technique in the construction of high-quality Bansuris.
Quality control and testing: Each bamboo flute is tested for playability, tone quality, and intonation. Adjustments are made to ensure the flute meets quality standards. World class standards are followed at Shashank Giri flutes while tuning the flute. very high precision tuners are used in tuning of the flute at our facility. After making the holes on the bamboo, the flute is kept untouched at least for a day for the flute to come to room temperature. Then the flute is picked up for fine tuning.